
Predictive Maintenance
Forecast the future
In today’s globalized marketplace, preventative maintenance may not be enough to ensure asset reliability in manufacturing, logistics, and operations. Strategies like scheduled checks and condition-based maintenance may not be sufficient to prevent damage to the system, product quality, process safety, or other consequences from aging or failing assets. Building the capacity to predict asset failure and prevent it is crucial. Predictive maintenance offers numerous business-critical advantages, making it an essential approach for managing assets effectively.
Industrial automation is rapidly growing due to IoT technologies, reduced data storage costs, and AI/ML advancements. However, maintenance organizations have not fully utilized these technologies. Ensuring asset maintenance involves limiting downtime, maximizing asset usage, and driving efficiency in maintenance. This applies to both manufacturing plants and field assets. Effective maintenance may have a greater business value than asset uptime.
Business value of effective maintenance:
Limiting fallout:
The enterprise can prevent cascading impacts that could slow other operations and lead to costly outages by anticipating and avoiding machine failures.
Elevating ROI:
Preventing failure can extend the lifespan of machines and assets, enabling businesses to maximize the value of their existing investments.
Empowering the workforce:
Preventing machine failures allows the maintenance workforce to focus on anticipating and preventing future issues, maximizing the use of valuable human capital.
Supporting procurement:
Knowing when a replacement part is needed enhances procurement, planning, timing, and sourcing in the face of supply chain disruptions. It also helps limit spare equipment on site and reduces business capital tied up in unneeded parts.
Improving safety:
Predicting and preventing machine failures can enhance the safety of enterprise operations by preventing potential harm to employees, assets, and overall production.
Improving quality control:
Assets nearing failure can negatively impact product quality, while proactive intervention and maintenance can enhance quality control.
Managing environmental impact:
Efficient maintenance practices, including replacing parts and supplying shop supplies, reduce waste and positively impact the environmental footprint of operations.
Improved productivity:
By minimizing downtime and optimizing asset performance, maintenance organizations can help increase overall productivity and efficiency.
Competitive advantage:
Organizations that effectively leverage advanced technologies in maintenance can gain a competitive advantage in their industry, differentiating themselves from competitors and improving their market position.
Predictive maintenance can improve business outcomes by identifying suitable technologies and process changes. Effective maintenance extends beyond asset uptime, unlocking benefits such as enhanced efficiency and reduced costs through the use of advanced technologies.
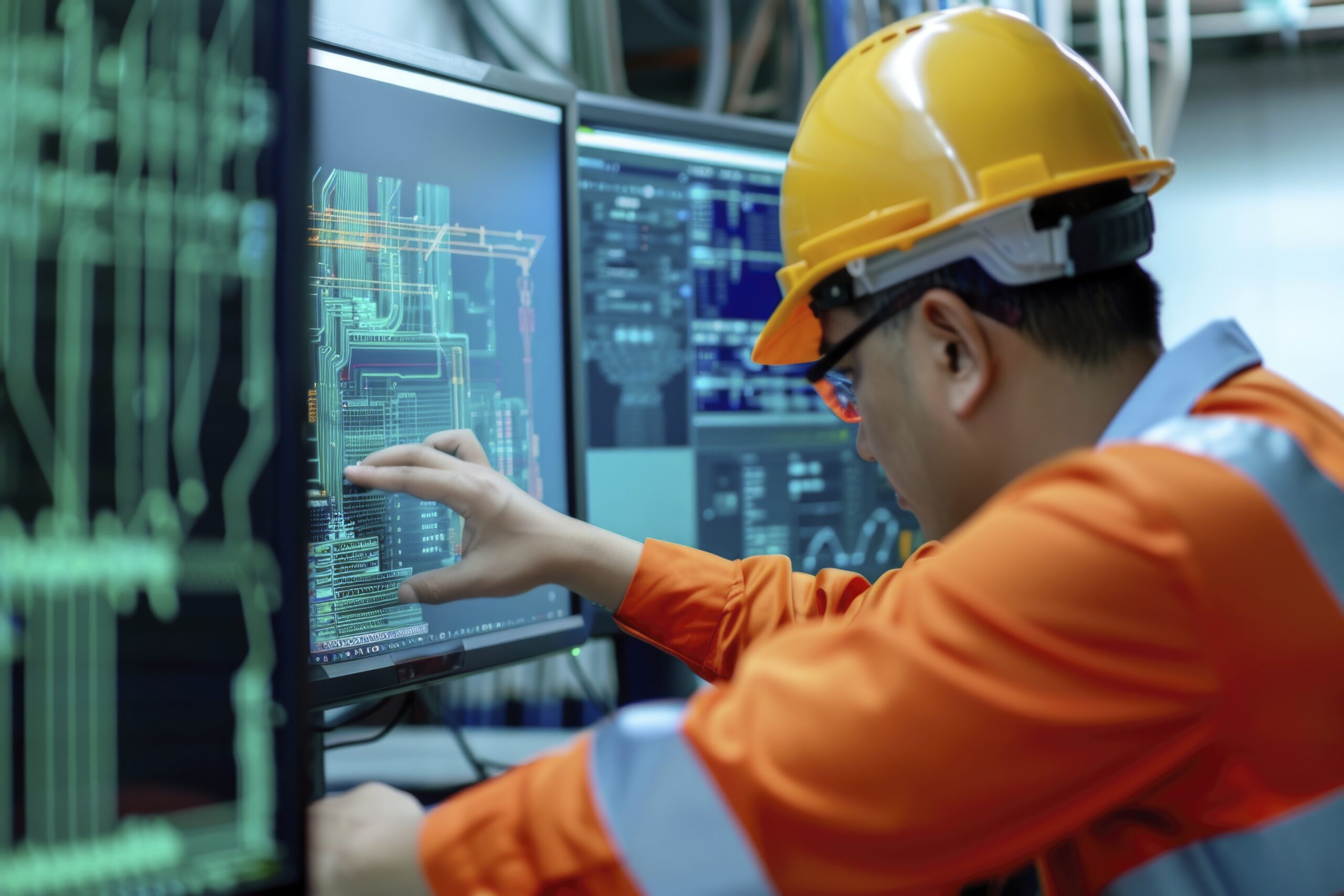
Using AI to help predict the future.
Maintenance schedules can be improved by replacing educated guesses with data-based knowledge about an asset’s performance and degrade date. This can be achieved by incorporating additional data sources, such as sensors, procurement and ERP data, historical maintenance and repair data, production data, and ongoing reports from field employees. By incorporating these sources, enterprises can unlock value and improve maintenance operations, ultimately leading to more efficient and effective maintenance.
By combining and analyzing data, AI-enabled signal processing may provide more in-depth knowledge of interdependent assets. Businesses can utilize the collective knowledge of people, sensors, and systems to evaluate information and provide maintenance suggestions that can be prioritized, therefore improving human workforce allocation. Businesses and assets vary, so assessing maintenance maturity is crucial to identifying areas where AI analysis can improve operations. While transforming to predictive maintenance may not be a one-time solution, some organizations may test new capabilities in a pilot program. With evidence of its benefits, businesses can seek other use cases, scale the program, and promote adoption across the enterprise.
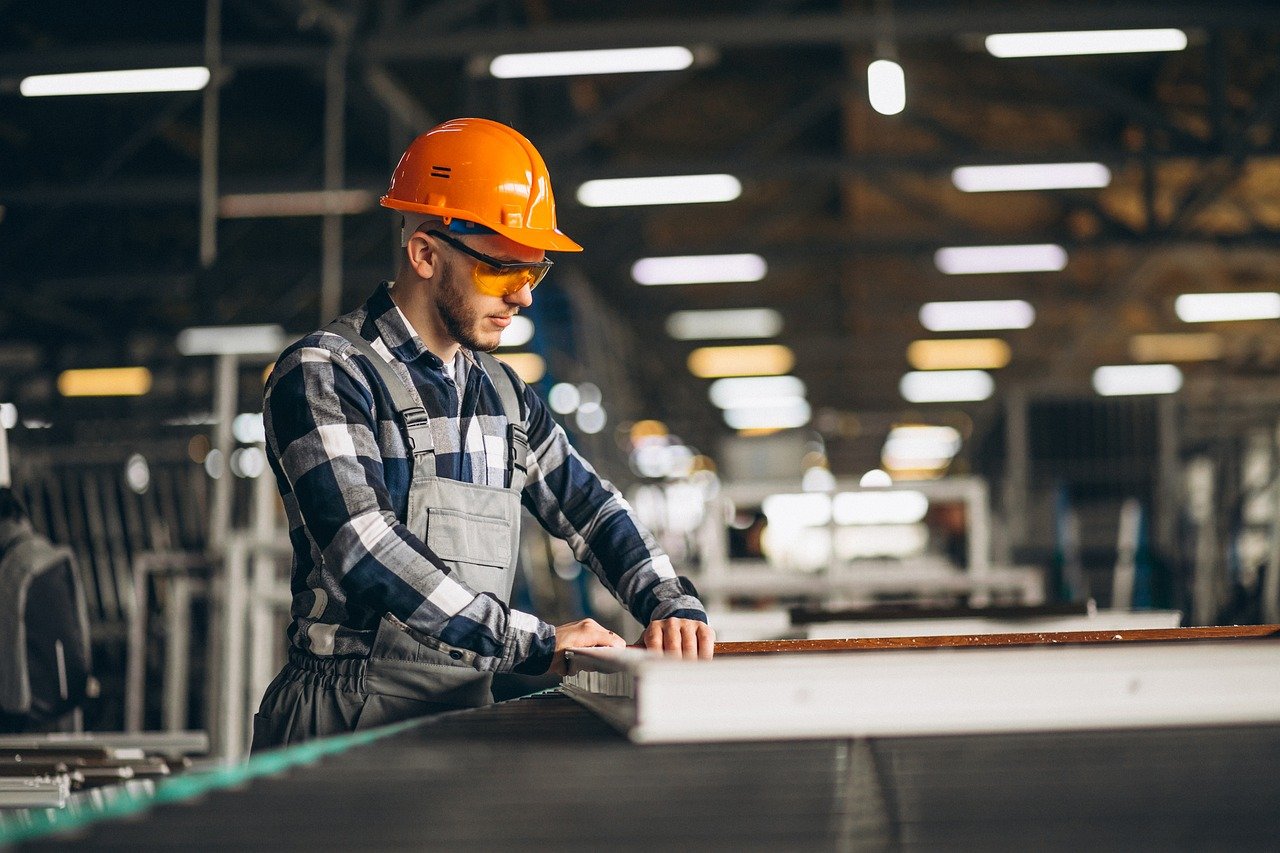
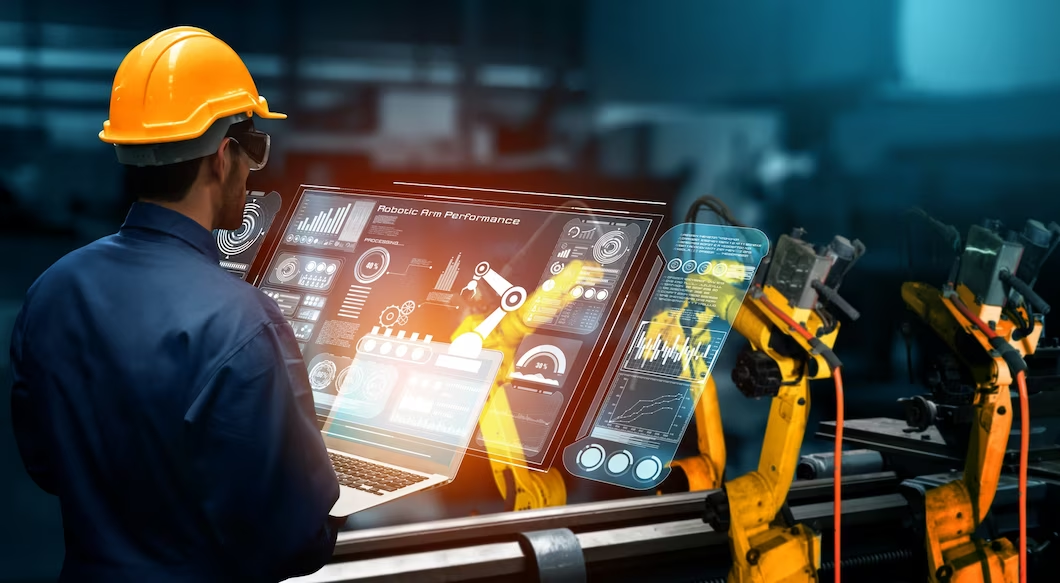
To fully utilize industrial automation and advanced technologies, maintenance organizations must develop a comprehensive strategy for integrating these technologies into their operations. This requires a deep understanding of the business value of effective maintenance and a commitment to leveraging technology for innovation and improvement. Key steps include:
Develop a clear business case. Establish a clear understanding of the business value of effective maintenance and the potential benefits of leveraging advanced technologies.
Assess current capabilities: Evaluate current maintenance processes and capabilities to identify areas for improvement and opportunities for technology adoption.
Develop a technology roadmap: Create a roadmap for implementing and integrating advanced technologies, including IoT, AI/ML, and data analytics.
Invest in training and development: Provide training and development opportunities for maintenance personnel to ensure they have the skills and knowledge needed to effectively leverage advanced technologies.
Monitor and evaluate progress: Regularly monitor and evaluate the effectiveness of maintenance operations and the impact of advanced technologies on business performance.
By taking these steps, maintenance organizations can move beyond pilots and fully harness the power of industrial automation and advanced technologies to drive innovation, improvement, and business success.